Dernière mise à jour le 07/03/2005
Au début, j'ai essayé d'utilisé un moteur synchrone à 750 tr/mn et de
multiplier sa vitesse par 4 à l'aide de 2 poulies et d'une courroie pour obtenir la
vitesse de 3000 tr/mn. Mais ce fut un échec car le moteur n'était pas assez puissant et
était incapable d'entrainer le multiplicateur de vitesse.
Je me suis donc rabattu sur un moteur asynchrone tournant à 2850 tr/mn et je
vais tenter de le modifier pour le rendre synchrone au secteur pour obtenir la vitesse de
3000 tr/mn. Cette modification consiste à effectuer 2 plats sur le rotor.
Pourquoi y a t'il synchronisation ? Dans le rotor il y a un champ
magnétique tournant. Ce champ magnétique a les mêmes caractéristiques sinusoïdal que
le courant électrique. C'est à dire qu'il présente a un endroit un maxi (pole nord par
exemple) puis un nul et ensuite un autre maxi (pole sud). C'est un peu comme si le stator
était remplacé par un aimant qui tourne autour du rotor. Ces deux maxis nord et sud, et
opposés, vont se caler sur les deux endroits où l'entrefer (l'espace) entre le rotor et
le stator sont minis. Il y aura donc synchronisation.
Attention ! : A la vitesse de 3000 tr
/mn, les forces centrifuges engendrées par la rotation deviennent importantes. Après calcul grâce
à la formule suivante Fc= mV2/R avec un diamètre de 20 cm, j'arrive à une
multiplication de la masse par 1000 !. Ce qui
veut dire que mes petits bouts de tungstène formant les contacts et qui pèsent 6g
verront leur masse passer à 6 kg ! Il faut donc que le disque qui les supporte soit
résistant.
Pour cela j'ai utilisé de l'époxy utilisé pour faire
des circuits imprimés. C'est un mélange de tissu de fibre de verre et de résine époxy
très résistant. De plus ce matériau résiste bien à la température. Bien que ...
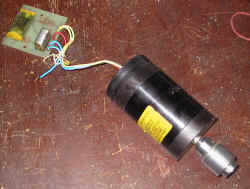
Moteur synchrone 750 tr/mn, mais pas assez puissant pour multiplier sa vitesse par 4.
|
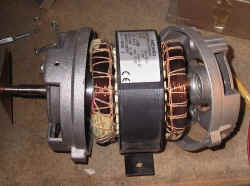
Ouverture de l'autre moteur asynchrone que je vais tenter de modifier. |
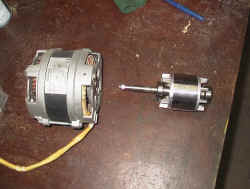
Le moteur démonté.
Le stator et le rotor avant modification |
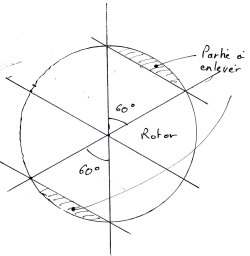
Les secteurs a découper sont égaux à 1/6 de la circonférence.
|
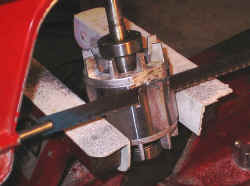
Découpe du premier plat sur le rotor.
|
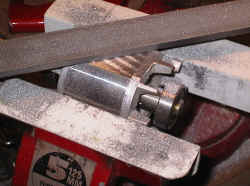
Ajustage à la lime.
Il est nécessaire d'obtenir une parfaite symètrie des deux plats pour éviter les
balourds. L'idéal serait de réaliser ceci à la fraiseuse...Mais un bon ajusteur y
arrivera sans problème.
|
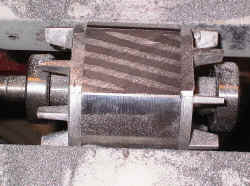
Résultat obtenu.
Remarquez la "cage d'écureuil" à l'intérieur.
|
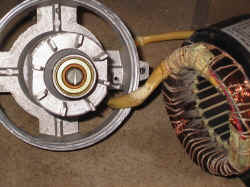
Réalisation du second plat et remontage du rotor.
|

Détail sur l'intérieur du stator
|
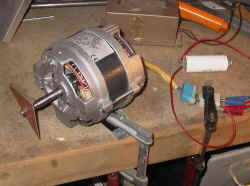
Premiers essais
La synchronisation est correcte et le démarrage sans problème. Le courant
absorbé est juste un peu plus important occasionnant un échauffement un peu plus
important mais sans conséquence pour le moteur.
|
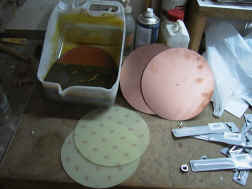
Fabrication du disque qui portera les contacts rotatifs du rupteur à l'aide de 6 plaques
d'époxy de circuit imprimé que je collerai ensemble. Ici j'enlève le cuivre avec du
perchlorure de fer.
|
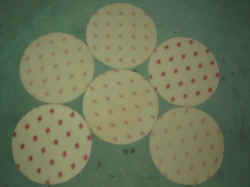
Les 6 disques de 1,5 mm d'épaisseur soit 9 mm au total.
Ensuite collage des 6 disques d'époxy ensembles avec de la résine époxy que j'applique
sur chaque face avec un petit rouleau de peintre. Attention avant
d'appliquer la résine, les disques doivent être dépolis avec du papier abrasif.
L'ensemble est ensuite mis sous presse pendant 24 h entre 2 surfaces parfaitement plane.
|
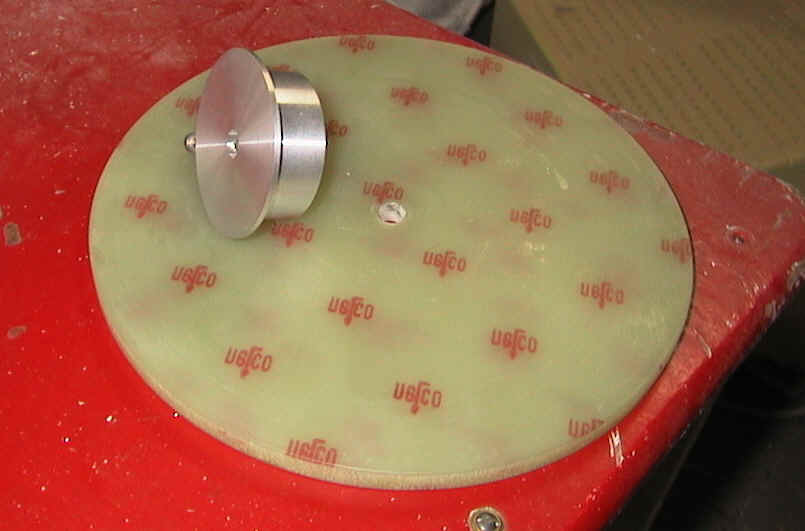
Résultat obtenu après avoir retouché le diamètre au tour pour qu'il tourne
parfaitement sans vibration. N'oublions pas que l'ensemble tournera à 3000 tr/mn.
Réalisation en aluminium de la flasque qui portera le disque sur l'axe du moteur.
|
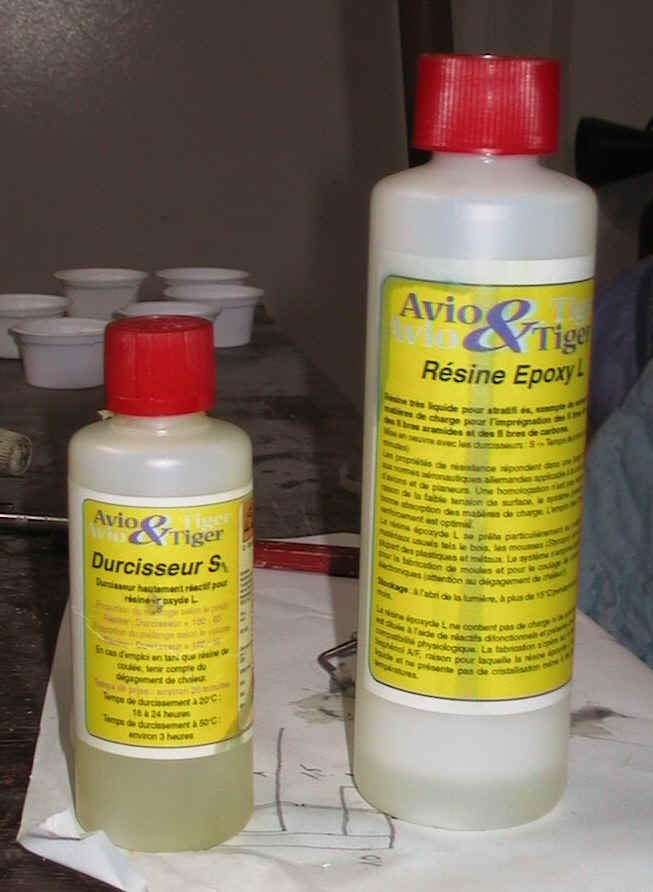
La résine que j'utilise pour le collage provient d'un magasin de modélisme.
|
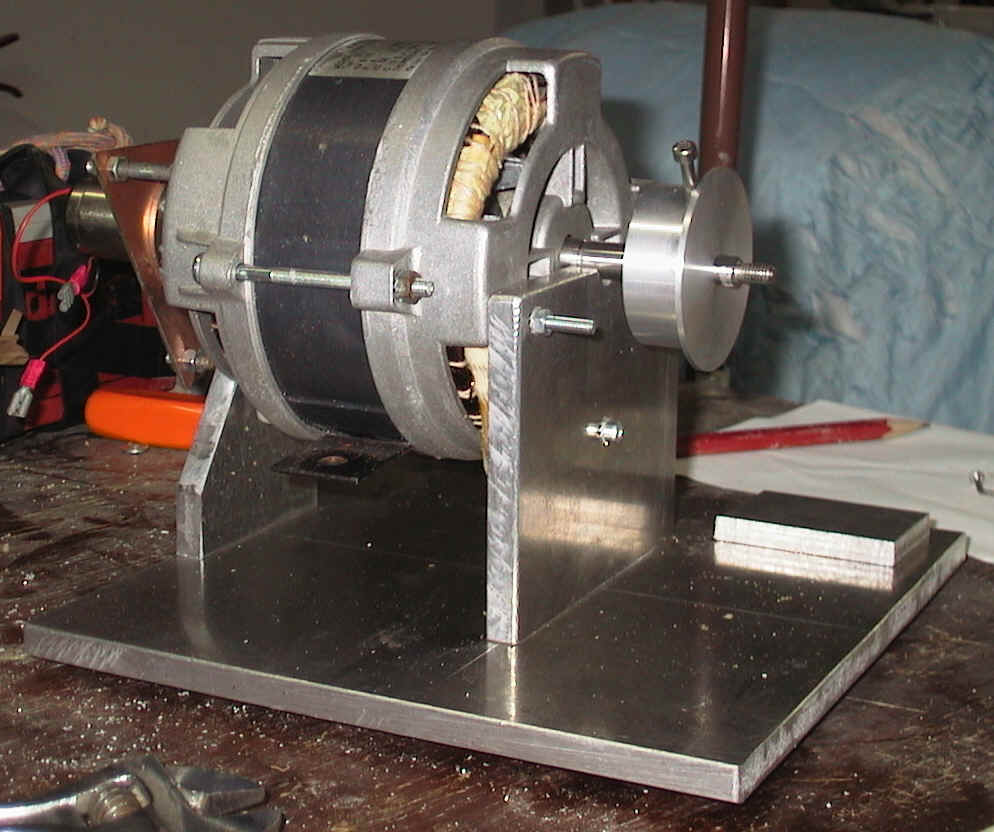
Réalisation du berceau que je ne décris pas car il sera différent suivant le type de
moteur que vous utiliserez. Sachez seulement qu'il devra être robuste pour éviter qu'il
ne bouge pendant la rotation.
|
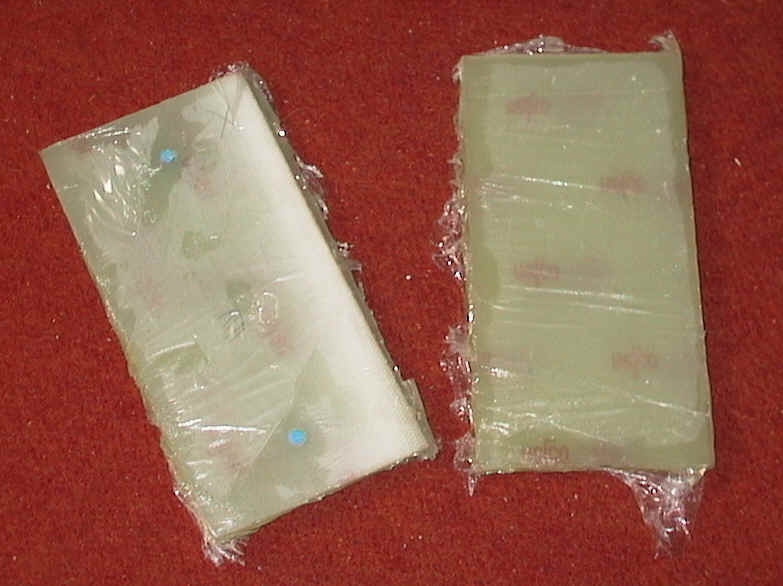
Réalisation de deux plaques en époxy de 10 cm par 5 cm qui supporteront les contacts
fixes. La technique est la même que pour le disque pour réaliser l'épaisseur voulue. Le
film plastique évite que la colle ne prenne sur la presse.
|
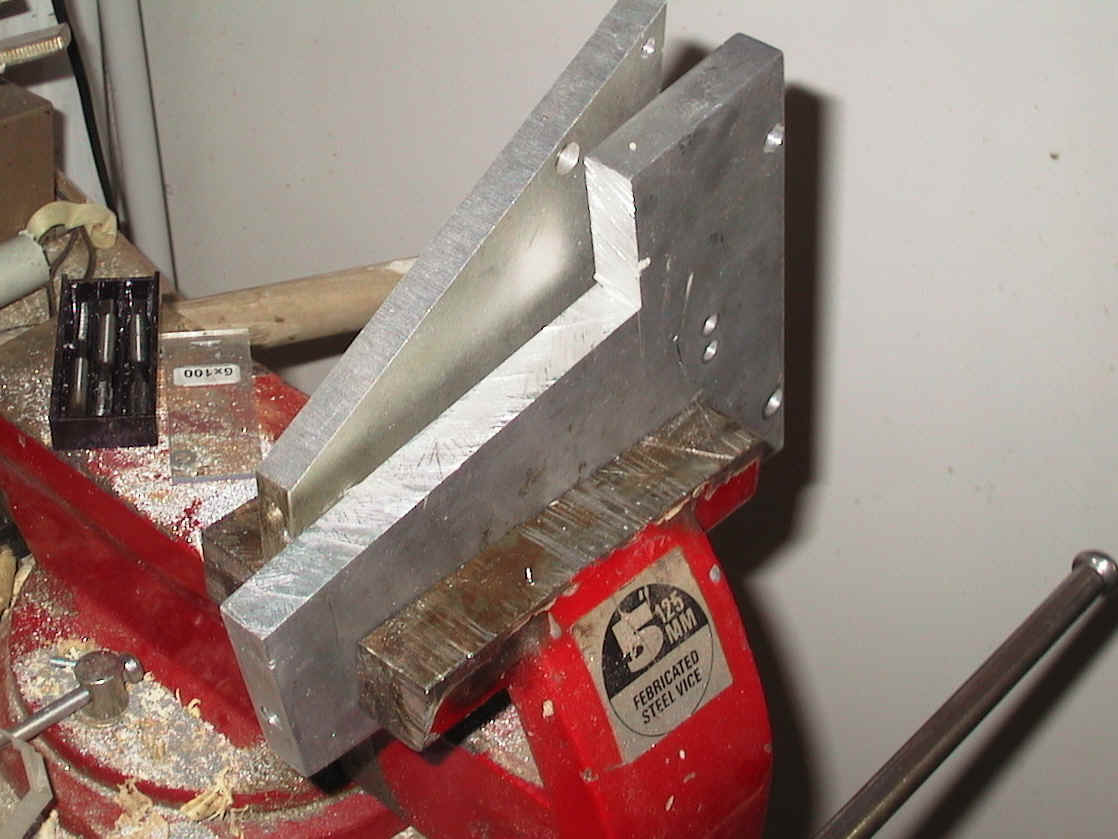
Voici une façon de serrer les plaques ensembles. Les plaques d'époxy se trouvent entre
deux morceaux d'aluminium parfaitement plan.
|
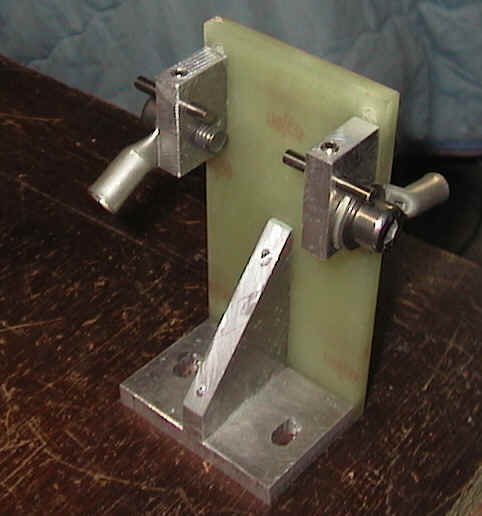
Et voici après avoir réalisé différentes petites pièces, un jeu de contacts fixes.
|
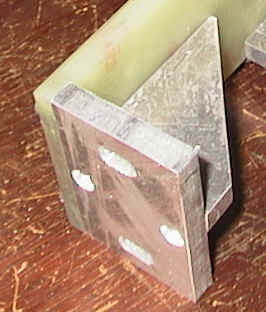
La semelle est en aluminium de 8 mm avec un gousset de même épaisseur. Les vis de 4 mm
du gousset sont noyées dans la semelle.
|
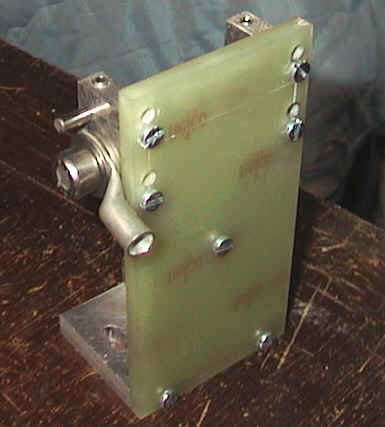
Les fixations sont réalisées avec des vis de 4 mm.
|
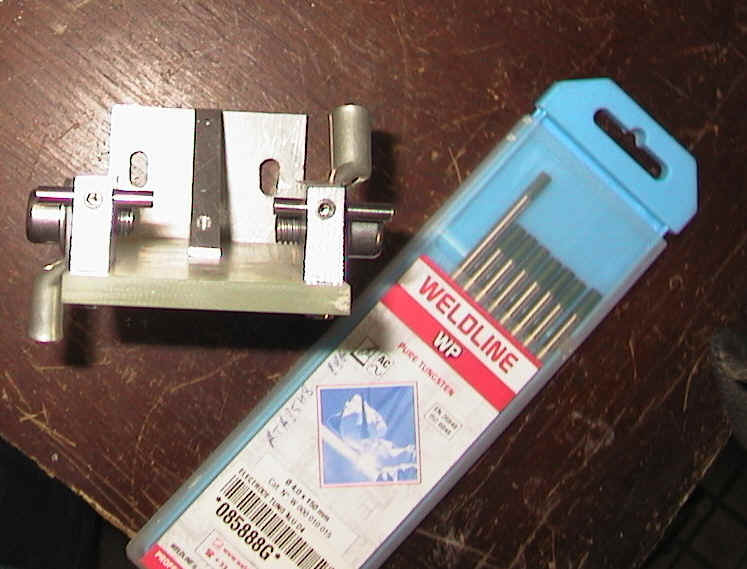
Les contacts de 4 mm sont en tungstène. Une vis pointeau de 5 mm immobilise le contact
dans son support. Les supports sont en aluminium de 8 mm d'épaisseur. les tige de
tungstène sont des électrodes pour la soudure TIG de diamètre 4 mm. Pour couper les
électrodes, utiliser une disqueuse puis redresser les extrémités à la meule.
|
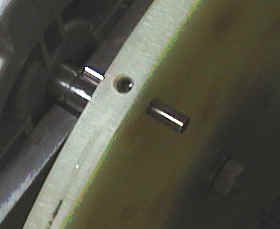
Mise en place de deux contacts de 25 mm sur le disque. Une vis pointeau de 5 mm immobilise
le contact sur le disque
|
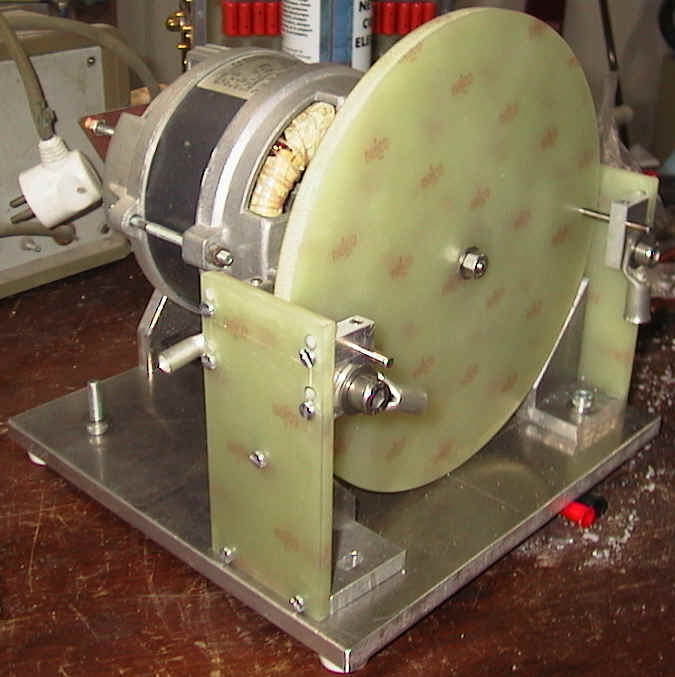
Et voici la partie mécanique du rupteur rotatif terminé. Il reste à le câbler et à
faire les réglages. L'écartement entre les contacts doit être le plus faible possible.
Les deux jeux de contacts mobiles doivent être parfaitement ensemble devant les contacts
fixes.
|
Une
partie du réglage consistera à le caler par rapport au réseau 50 Hz de façon que la
fermeture des électrodes se fasse au maximum de l'alternance positive et négative. Voir les réglages
Ensuite deux vis viendront bloquer le réglage dans la bonne position. |
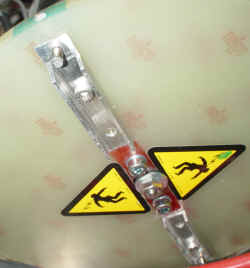
Suite à un échauffement excessif des contacts commençant à brûler l'époxy,
j'ai rajouté 4 radiateurs supplémentaires recto verso sur le disque pour améliorer le
refroidissement des contacts. Nous remarqueront aussi le blocage du disque sur son axe par
2 vis BTR M5
|
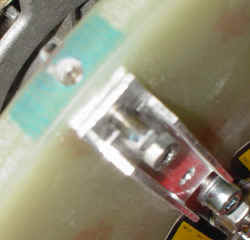
Ce sont 4 morceaux de profilé en U en aluminium qui sont percés juste au
diamètre des tiges de tungstène. Fixé par 2 vis BTR et écrou Nylstop. J'ai aussi
rajouté un petit tube d'aluminium autour de la tige de tungstène pour encore améliorer
l'échange thermique. Le refroidissement est maintenant efficace.
|
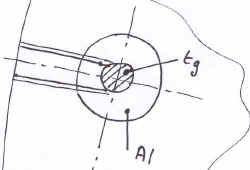
Détail du tube d'aluminium autour de la tige, noyé dans le disque époxy.Il
est nécessaire de peser les différents accessoires au 1/10 de grammes près et de les
positionner précisément sur le disque époxy pour éviter les balourds et vibration. |
Après plus de 20 heures de rotation. je n'ai rencontré aucun problème avec cet éclateur rotatif.
Il me donne entière satisfaction. Les contacts sont toujours ceux d'origines et s'usent très peu. |